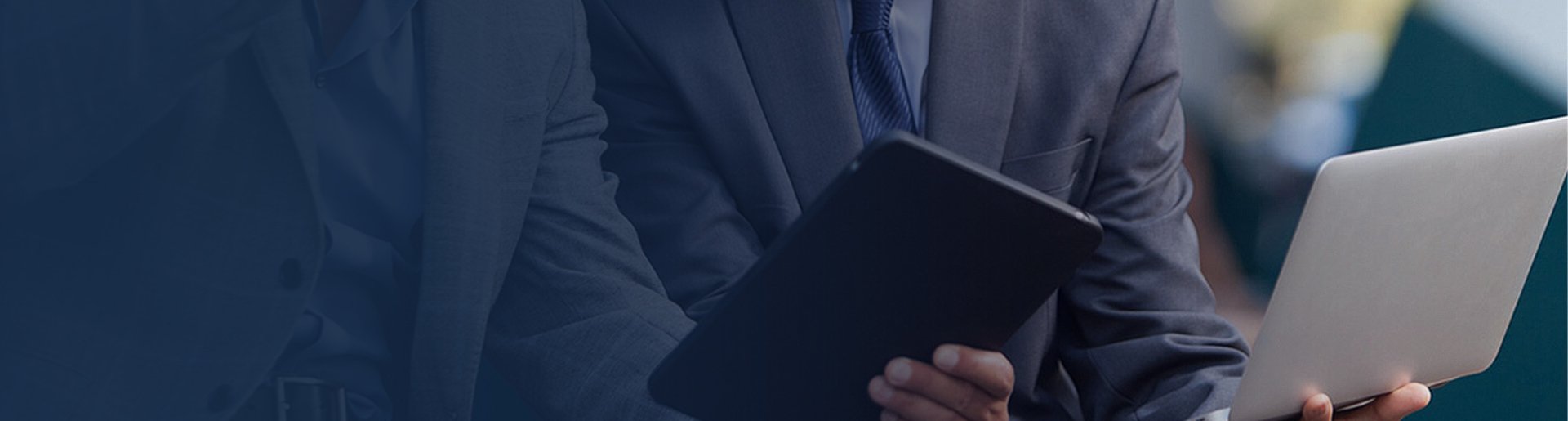
Use process and production data management of stamping parts
There are many advantages in using cold extrusion process to process stamping parts, but in the process of use, hardware stamping parts manufacturers still have some problems. Now let's understand what these difficulties are.
1. Due to the high cost of the cold extrusion die, it is generally only applicable to the parts produced in large batches, and its suitable small batch is 50000~100000 pieces;
2. Large tonnage press is required. Due to the large deformation resistance of the blank during cold extrusion, hundreds of tons or even thousands of tons of presses are required;
3. The blank needs surface treatment before extrusion, which not only increases the working procedure, takes up a large production area, but also is difficult to achieve production automation;
4. The plasticity and impact toughness of cold extruded parts become worse, and the residual stress of the parts is large, which will cause the reduction of part deformation and corrosion (stress corrosion);
5. High requirements for moulds. During cold extrusion, the blank is subjected to three compressive stresses in the die, which significantly increases the deformation resistance. This makes the stress on the die much larger than that on general metal stampings. During cold extrusion of steel, the stress on the die often reaches 2000MPA~2500MPA; Therefore, in addition to the need for mold, it also needs to have enough impact toughness and performance. In addition, the strong plastic deformation of the metal blank in the mold will raise the mold temperature to about 250 ℃~300 ℃, so the mold materials need corresponding tempering stability. According to the above situation, the service life of cold extrusion die is far lower than that of cold metal stamping parts.