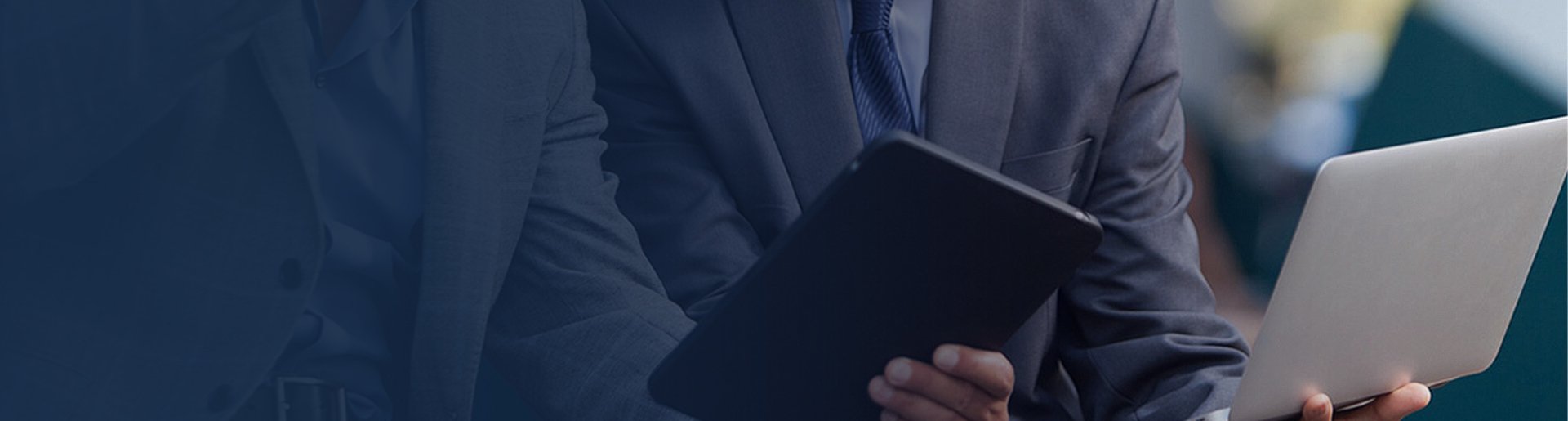
The application of deep drawing technology in actual production
In practical production, deep drawing technology has a wide range of applications. For example, in the automotive manufacturing industry, the manufacturing of components such as engine oil pans and body coverings cannot be separated from deep drawing technology. Taking the engine oil pan as an example, its shape is complex and requires high dimensional accuracy and surface quality. During the manufacturing process, it is necessary to select the appropriate mold type and process parameters based on the specific shape and size of the oil pan. Firstly, determine a reasonable deep drawing coefficient, gradually form the oil pan through multiple deep draws, and accurately control parameters such as edge pressure and deep drawing speed to ensure the quality of the oil pan. In the field of daily necessities manufacturing, products such as stainless steel pots and cans are also widely produced using deep drawing technology. During the deep drawing process of stainless steel pots, it is necessary to consider the thickness and shape requirements of the pot bottom, as well as the uniformity of the thickness of the pot wall. The deep drawing of cans requires high thickness and performance of the material, as well as strict requirements for the accuracy and production efficiency of the deep drawing.
In order to ensure the quality of deep drawn workpieces, strict quality control and testing are required during the production process. In terms of quality control, real-time monitoring and adjustment of process parameters such as edge pressure and deep drawing speed are used to prevent defects such as wrinkling and tearing. At the same time, regular inspections and maintenance are carried out on the accuracy and surface quality of the mold to ensure its normal operation. In terms of inspection, visual inspection is used to check whether there are defects such as cracks and wrinkles on the surface of the workpiece; Using non-destructive testing techniques such as ultrasonic testing, magnetic particle testing, etc., to detect whether there are defects inside the workpiece. For the dimensional accuracy of the workpiece, precision measuring instruments such as coordinate measuring machines are used to ensure that the dimensions of the workpiece meet the design requirements. If any size deviation is found, adjust the mold or process parameters in a timely manner for correction.