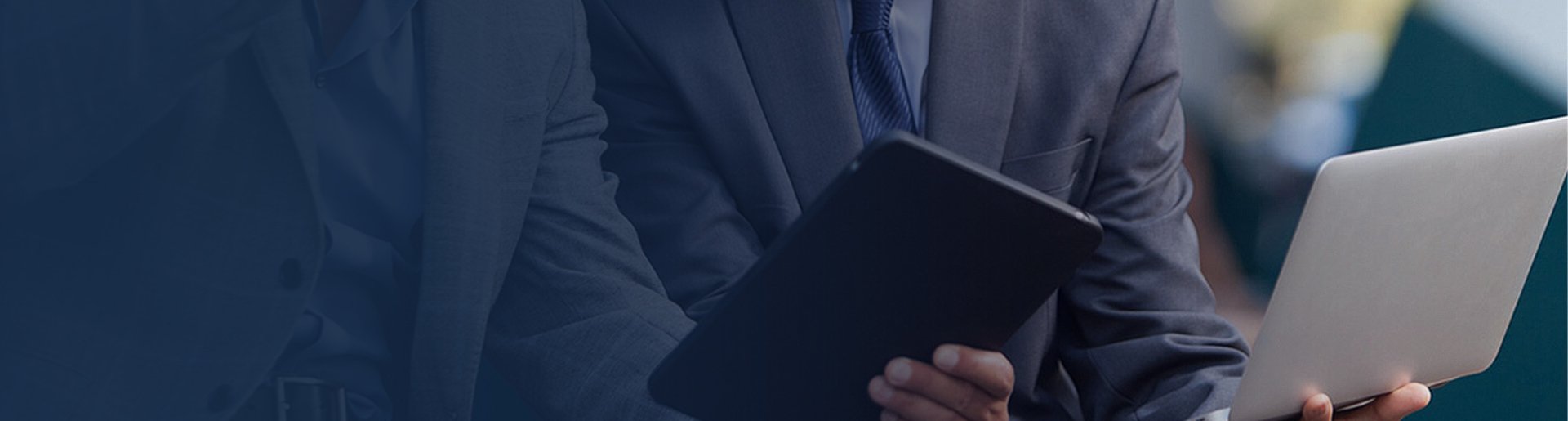
What are the ways of metal deep drawing
In deep drawing and stamping processes, various forming operations are typically required to complete component fabrication. These critical operations include:
1. Beads, Ribs, and Flanges: These structural features are strategically implemented to enhance rigidity in components that may exhibit excessive flexibility or fragility. Their optimized application can reduce required material thickness by up to 50%.
2. Bulging: A process utilizing segmented punches with internal expansion mechanisms or pressure mediums (compressed air, hydraulic fluid, semi-liquids, rubber, or elastomers) to radially deform cup walls, shells, or tubular sections. Achievable in both axisymmetric and asymmetric configurations.
3. Coining: A closed-die compression operation enforcing strict constraint on all workpiece surfaces to achieve dimensional precision and surface refinement.
4. Crimping: Formation of rolled edges at component apertures through controlled plastic deformation.
5. Countersinking: Localized indentation forming to create flush-mounted surfaces for fastener heads (rivets/bolts).
6. Embossing: Shallow relief patterning generation with negligible material thickness variation, typically for decorative or functional surface texturing.
7. Extruding/Hole Flanging: Peripheral material displacement around pre-pierced apertures to create reinforced flanges, also termed "hole expansion."
8. Piercing: Material removal from drawn components using conventional, extruded, or specialized punch geometries to create functional openings.
9. Ironing: Precision wall thickness reduction with simultaneous surface finishing through controlled radial compression.
10. Marking: Permanent impression of alphanumeric identifiers, logos, or technical markings on component surfaces.
11. Necking: Controlled diameter reduction in cylindrical shell segments through progressive forming.
12. Notching: Precision edge profiling for mechanical clearance, assembly alignment, or interconnection features.
13. Threading: Generation of helical fastening features using roller dies, taps, or thread-forming mandrels.
14. Trimming: Final contour definition through excess material removal along predetermined trim lines.
This operational taxonomy represents essential methodologies in advanced sheet metal forming, requiring precise control of material flow, strain distribution, and tooling interactions to achieve specified mechanical properties and geometric tolerances.
If you want to learn more, you can click to read the following content or contact us. Custom Metal Deep Drawing Parts