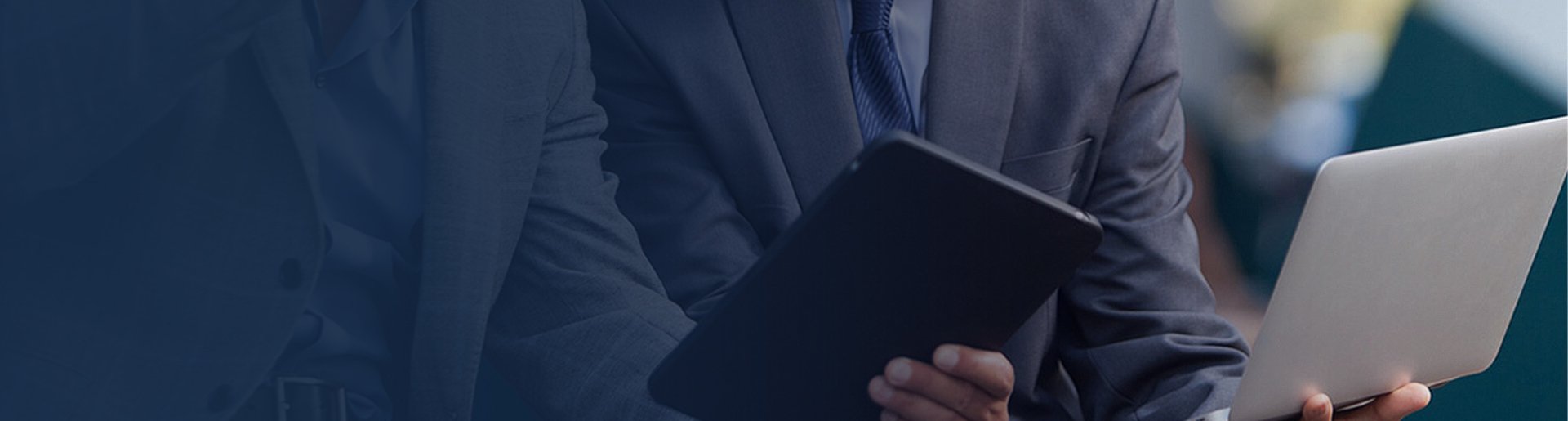
How to choose between metal deep drawing or metal stamping for customized metal parts
How to choose between metal deep drawing or metal stamping for customized metal parts
When evaluating the choice between deep-drawn metal parts and metal-stamped parts, several critical considerations arise, rooted in the technical and economic characteristics of these metal-forming processes.
Metal stamping is a cost-effective manufacturing technique suitable for producing a wide range of components. This process involves placing sheet metal into a press operated by a trained stamping technician, where dies shape the material through controlled force. While metal-stamped parts generally offer lower production costs, their design complexity is constrained by the limitations of the stamping dies and the incremental forming nature of the process.
In contrast, deep drawing is a specialized sheet metal forming process that achieves significant three-dimensional deformation. It entails using a punch with a rounded edge to mechanically press a metal blank into a contoured die, creating components with substantial depth relative to their diameter—a defining characteristic known as radial stressing. The material is plastically deformed to conform to the die’s geometry, resulting in a seamless, smooth-surfaced part with curved or complex profiles. Unlike traditional stamping, which often relies on multiple blanks or progressive steps, deep drawing typically forms parts from a single metal blank, minimizing assembly requirements and enhancing structural integrity.
Key differentiators between the two processes include surface finish and design versatility. Deep-drawn parts exhibit a continuous, weld-free surface, making them ideal for applications requiring aesthetic precision or fluid dynamics optimization, such as automotive oil filters, aluminum beverage cans, jet engine components, and lighting reflectors. The process accommodates intricate geometries and tight tolerances, enabling the production of lightweight yet robust components with high strength-to-weight ratios. Industries such as aerospace, automotive, pharmaceuticals, dairy, and plastics leverage deep-drawn parts for their durability and form complexity, particularly in environments demanding resistance to corrosion, high temperatures, or mechanical stress.
Deep drawing is particularly advantageous for both large-scale bulk production and smaller runs of long-life components, as tooling investments can be amortized over extended use. Material compatibility is another strength, with suitable metals including alloys, aluminum, brass, cold-rolled steel, copper, invar, iron, kovar, molybdenum, nickel, silver, stainless steel, and tungsten. These materials exhibit the ductility and formability necessary to withstand the intense plastic deformation involved in deep drawing while maintaining dimensional stability and mechanical properties.
In summary, while metal stamping excels in cost-efficient production of simpler geometries, deep drawing offers unmatched capabilities for creating seamless, complex, and high-performance components across diverse industrial applications, supported by a broad range of material options and scalable manufacturing capacity.