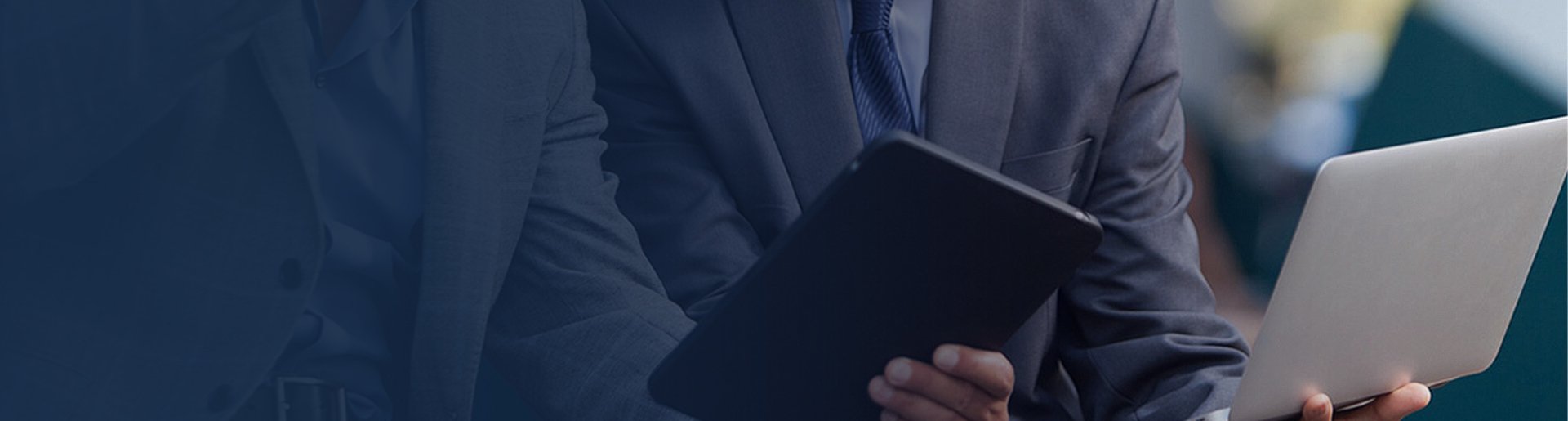
The process of deep drawing technology
During the deep drawing process, different regions of the blank exhibit different deformation characteristics. The central part of the billet eventually becomes the bottom of the simple part, and this area is basically not deformed, which can be regarded as the non deformed zone. Although it does not produce plastic deformation, during the deep drawing process, the bottom area is subjected to pressure from the punch and tension from other parts of the billet. The balance of these forces is crucial for maintaining the stability of the deep drawing process and ensuring the accuracy of the final shape of the workpiece.
The flange part of the blank is the main deformation zone. During the deep drawing process, the material of the flange part undergoes plastic deformation under the combined action of tangential compressive stress and radial tensile stress. The tangential compressive stress causes the flange material to have a tendency to shrink towards the center, while the radial tensile stress gradually transfers the material towards the cylinder wall. As the deep drawing progresses, the diameter of the flange gradually decreases, and the material is continuously pulled towards the cylinder wall, causing the height of the cylinder wall to gradually increase. This stress-strain state can be analyzed through relevant theories in materials mechanics, such as using the concepts of principal stress and principal strain to describe the stress and deformation of materials during the deformation process.
If you want to customize metal deep drawing parts, please read the following article. Custom Metal Deep Drawing Parts