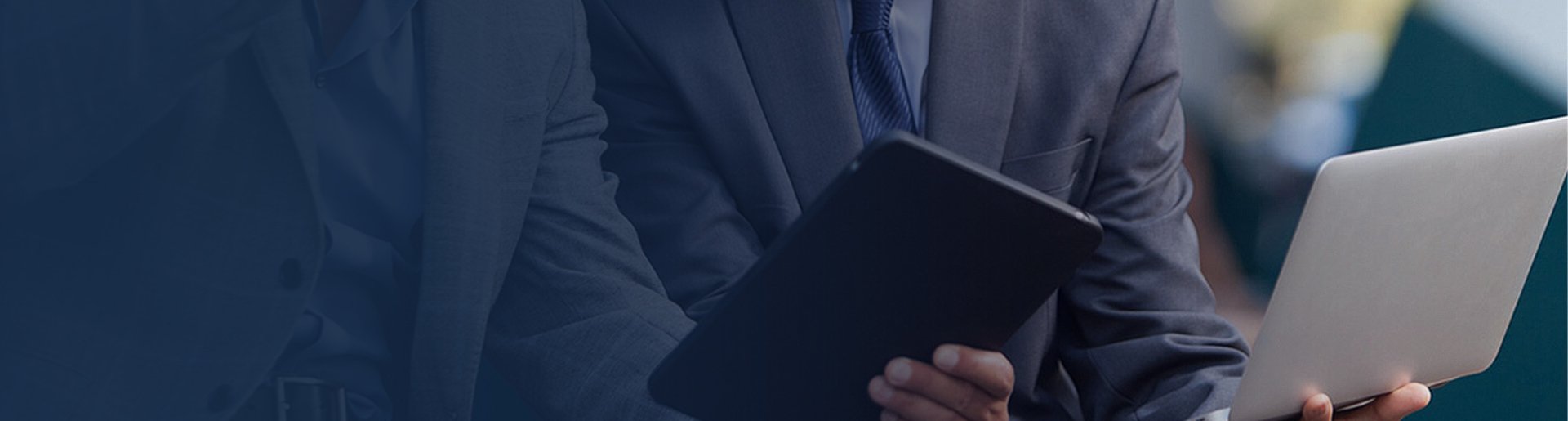
Destructive testing of welding processes in sheet metal manufacturing
Destructive testing of welding processes plays a vital role in sheet metal manufacturing. It is a method of evaluating welding quality and reliability through destructive testing of welded joints. This article will introduce in detail the destructive testing methods of welding processes commonly used in sheet metal manufacturing, including tensile testing, impact testing and hardness testing, as well as their principles, equipment and materials, advantages and disadvantages and application scope, to help readers deeply understand and apply this method. Key quality control techniques.
1. Tensile test:
Principle: Tensile test is to test the tensile strength and elongation of welded joints by applying tensile force. Usually, the welded parts are placed in a tensile testing machine, gradually increasing tensile force is applied until fracture occurs, and then the fracture is evaluated. Welding quality.
Equipment and materials: Including tensile testing machines, standard specimens and data recording equipment, etc.
Advantages and Disadvantages: It can directly measure the mechanical properties of welded joints, and the test results are accurate and reliable. It is suitable for various materials and welding processes; however, it requires special equipment and sample preparation, and the sample needs to be destroyed.
2. Impact test:
Principle: The impact test evaluates the toughness and impact resistance of the welded joint by applying impact load. An impact testing machine is usually used to impact the welded joint, and then the welding quality is evaluated based on the damage of the sample.
Equipment and materials: Including impact testing machines, standard specimens and data recording equipment, etc.
Advantages and Disadvantages: It can quickly evaluate the toughness and impact resistance of welded joints, and is suitable for various materials and welding processes; however, it has strict requirements on the shape and size of the specimen and requires destroying the specimen.
3. Hardness test:
Principle: Hardness testing is to evaluate the hardness of welded joints by applying a certain load on the surface of the welded joint and measuring the size or depth of the impression. Commonly used hardness testing methods include Brinell hardness test, Rockwell hardness test, etc.
Equipment and materials: Including hardness tester, standard specimen and data recording equipment, etc.
Advantages and Disadvantages: It can quickly evaluate the hardness of welded joints and is suitable for various materials and welding processes; however, it can only indirectly reflect the mechanical properties of welded joints, and the test results are greatly affected by the surface condition and shape of the sample.
Summarize:
Destructive testing of welding processes is an important means to ensure welding quality and safety in sheet metal manufacturing. Through the comprehensive use of tensile testing, impact testing, hardness testing and other methods, the mechanical properties and durability of welded joints can be comprehensively evaluated, and problems and defects can be discovered in a timely manner. Eliminate potential quality problems, improve the reliability and stability of the welding process, and ensure product quality and safety.