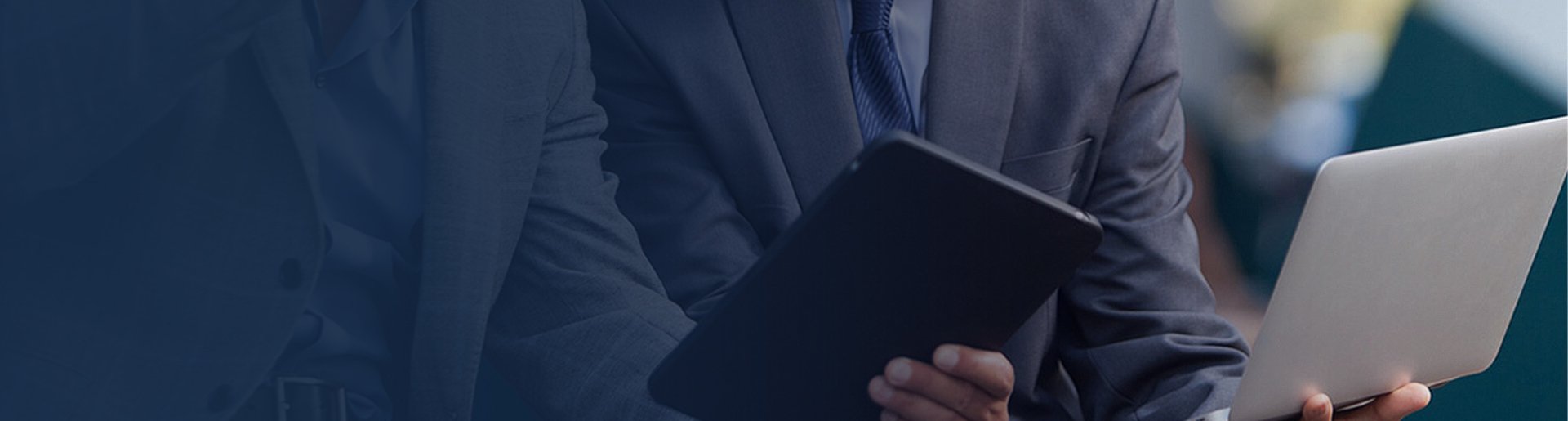
EDM cutting process
The EDM cutting process is a commonly used non-traditional cutting method, usually used to cut hard materials with low electrical conductivity, such as carbide, ceramics, quartz, etc. It uses the principle of electric spark discharge to generate electric sparks on the surface of the workpiece for cutting. This process has unique advantages and disadvantages, which are detailed below.
advantage:
High-precision cutting: EDM cutting has high cutting precision, which can achieve fine cutting of workpieces, with smooth cutting surface and precise cutting size.
Wide scope of application: EDM cutting is suitable for materials of various hardnesses, including metals, ceramics, quartz, etc., and has strong versatility.
Controllable cutting depth: EDM cutting can achieve precise control of the cutting depth by adjusting discharge parameters, such as discharge current, pulse interval, etc., and is suitable for scenes that require cutting depth.
No heat-affected zone: EDM cutting is a cold working method. There is no heat-affected zone during the cutting process, which will not cause problems such as deformation and hardening of the workpiece, and maintain the original properties of the workpiece material.
Non-contact cutting: EDM cutting is a non-contact cutting process that does not cause damage to the workpiece surface and maintains the integrity of the workpiece surface.
Fast cutting speed: EDM cutting can achieve faster cutting speed and is especially suitable for cutting materials with higher hardness.
Smooth cutting surface: The cutting surface of EDM cutting is smooth and has few burrs. It does not require subsequent surface treatment, saving processing procedures and costs.
shortcoming:
High equipment cost: The investment cost of EDM cutting equipment is high, and the maintenance and operating costs are also high, which requires certain capital investment from the manufacturer.
Slow cutting speed: Compared with traditional cutting methods, the cutting speed of EDM cutting is slower, especially for large-area cutting requirements, and the efficiency is low.
Not suitable for conductive materials: EDM cutting is mainly used for cutting hard materials with low conductivity and is not suitable for cutting of conductive materials.
High requirements for discharge parameters: EDM cutting operators need to have a high technical level and operating experience, and be proficient in adjusting discharge parameters and equipment operation skills to ensure cutting quality and safety.
Restricted cutting depth: EDM cutting has certain restrictions on the cutting depth and is not suitable for scenes that require high cutting depth.
High requirements on the shape of the workpiece: EDM cutting has high requirements on the shape of the workpiece and is not suitable for cutting workpieces with complex shapes.
High operating technical requirements: EDM cutting operators need to have a high technical level and operating experience, and be proficient in equipment operation and process parameter adjustment to ensure cutting quality and safety.
In summary, the EDM cutting process has the advantages of high precision and wide application range, but it also has shortcomings such as high equipment cost and slow cutting speed. It needs to be comprehensively considered in practical applications to select the appropriate cutting method to meet the processing of the product. need.