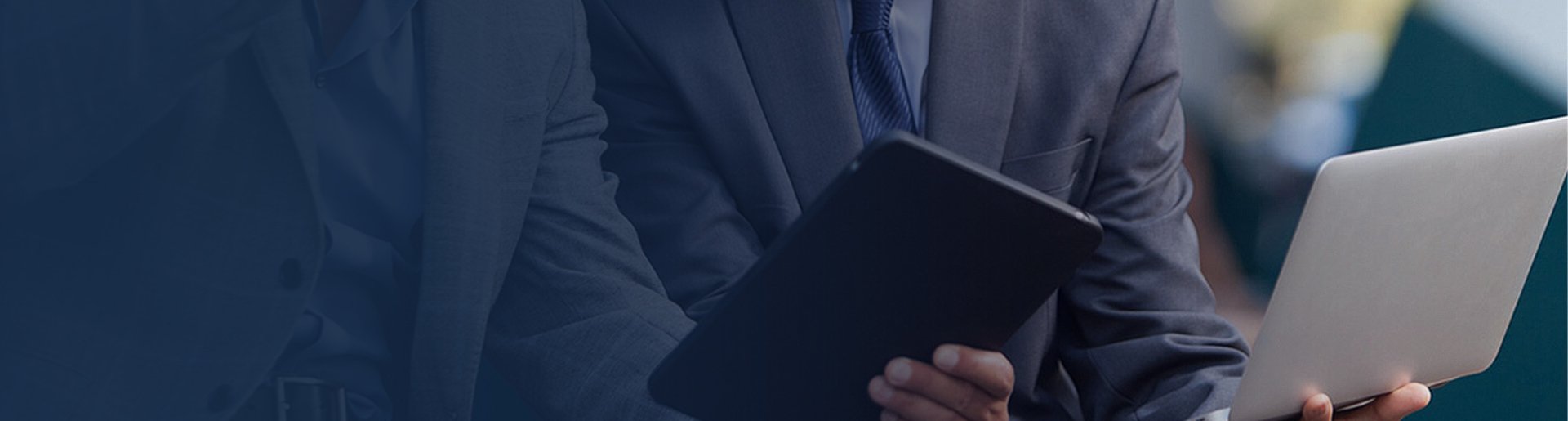
Internal cooling technology for stainless steel processing
Internal cooling technology for stainless steel material processing is an effective processing method. By providing cooling lubricant to the inside of the tool during the cutting process, it reduces the cutting temperature, cutting force and friction resistance, thereby improving processing efficiency and product quality. This article will introduce in detail the internal cooling technology of stainless steel materials in sheet metal manufacturing and its advantages and disadvantages.
1. Principle of internal cooling technology:
Sheet metal manufacturing internal cooling technology is to send cooling lubricant into the inside of the tool during the cutting process, so that it can directly cool the contact area between the tool and the workpiece, lower the processing temperature, reduce friction and wear, and improve processing efficiency and surface quality.
2. Advantages of internal cooling technology:
a. Improve cutting efficiency: Internal cooling technology can effectively reduce cutting temperature, reduce cutting force and friction resistance, increase cutting speed and feed speed, thereby improving processing efficiency.
b. Increase tool life: Internal cooling technology can effectively reduce the temperature of the tool, reduce tool wear and damage, extend the service life of the tool, and reduce processing costs.
c. Improve the quality of the machined surface: Internal cooling technology can reduce the accumulation of cutting heat, reduce the friction between the tool and the workpiece, reduce scratches and burrs, and improve the smoothness and accuracy of the machined surface.
d. Reduce the usage of cooling lubricant: Internal cooling technology can accurately control the usage of cooling lubricant, reduce waste and pollution, and reduce environmental pollution and costs.
3. Disadvantages of internal cooling technology:
a. Large equipment investment: Internal cooling technology requires specialized cooling systems and equipment, with high investment costs and certain requirements for the economic strength of the enterprise.
b. Requires professional maintenance: Equipment with internal cooling technology requires regular maintenance and upkeep, such as replacing cooling lubricants, cleaning cooling pipes, etc., which requires professional technicians to operate and maintain.
c. Not applicable to all processing scenarios: Internal cooling technology has certain requirements on processing equipment and workpiece shape, and is not suitable for all processing scenarios. It needs to be selected and applied according to the actual situation.
4. Summary:
Internal cooling technology of stainless steel materials in sheet metal manufacturing is an effective processing method, which can improve cutting efficiency, increase tool life, improve machined surface quality, and reduce the use of cooling lubricants. However, there are also large equipment investments and the need for Disadvantages include professional maintenance and not being suitable for all processing scenarios. Therefore, when applying internal cooling technology, it is necessary to fully consider its advantages and disadvantages and make reasonable selection and application.