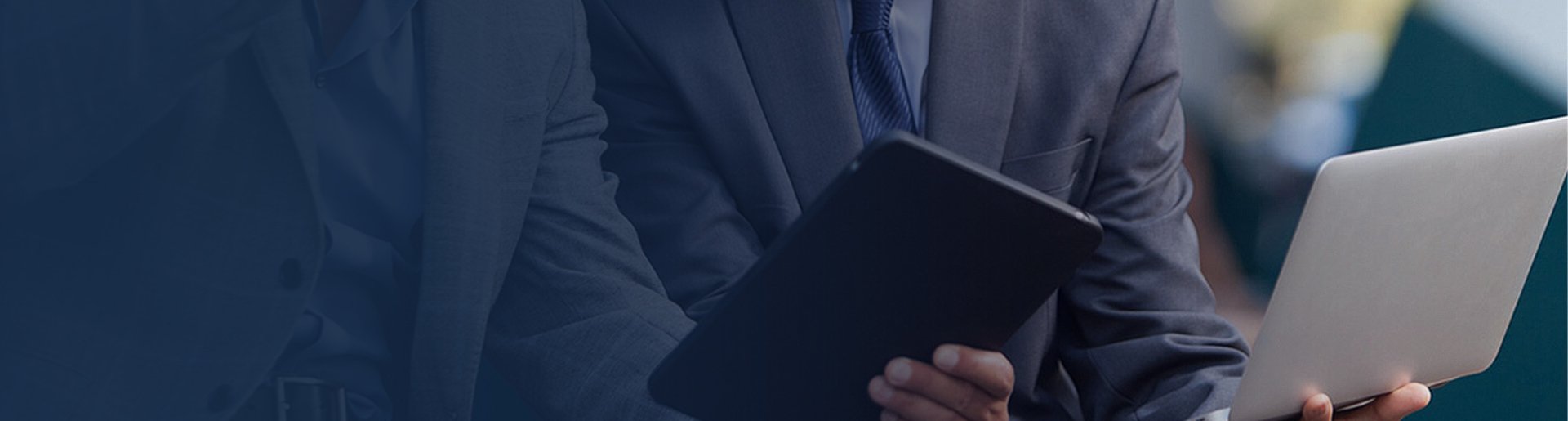
How to choose a high-quality metal bending pipe supplier
Qualification certification verification
Basic qualifications: Business license, production license (such as special equipment manufacturing license, applicable to pressure pipeline components).
Quality System Certification: ISO 9001 Quality Management System Certification, Industry Related Certification.
Proof of production capacity: Check the factory scale, equipment list (such as pipe bending machine type, heat treatment furnace, flaw detection equipment, etc.), and whether it has the process capabilities of cold bending, hot bending, pushing, etc.
Industry experience and reputation
Priority should be given to suppliers who have been deeply involved in the metal pipeline industry for more than 5 years, with a particular focus on their project experience in target fields such as petroleum, chemical, power, and construction.
3、 Evaluate product quality and testing capabilities
Quality Control System
Inquire with the supplier if they have a comprehensive quality control process, including raw material inspection (such as spectral analysis, material reports), production process testing (dimensional accuracy, surface quality), and finished product testing (hydrostatic testing, non-destructive testing (NDT), mechanical performance testing, etc.).
Request to provide product testing reports and material certificates (quality assurance certificates), and if necessary, entrust a third-party organization for re inspection.
Sample Testing
Before bulk procurement, it is required to provide samples and conduct actual testing:
Appearance inspection: No cracks, wrinkles, or uniformity of wall thickness.
Dimensional accuracy: meets the requirements of the drawing (such as bending radius error, angle deviation).
Performance testing: Conduct pressure resistance, corrosion resistance, fatigue testing, etc. according to the application scenario.
4、 Assess delivery and service capabilities
Production and delivery capability
Confirm whether the production capacity matches the demand, especially the response speed for bulk orders or urgent orders.
Technical support and after-sales service
Pre sales: Can you provide technical solution optimization suggestions (such as the impact of bending process on fluid resistance).
After sales: Quality problem handling process (return and exchange policy, compensation mechanism), technical consulting support during long-term use.
Value added services: whether to provide installation guidance, on-site surveying, customized molds as needed, etc.