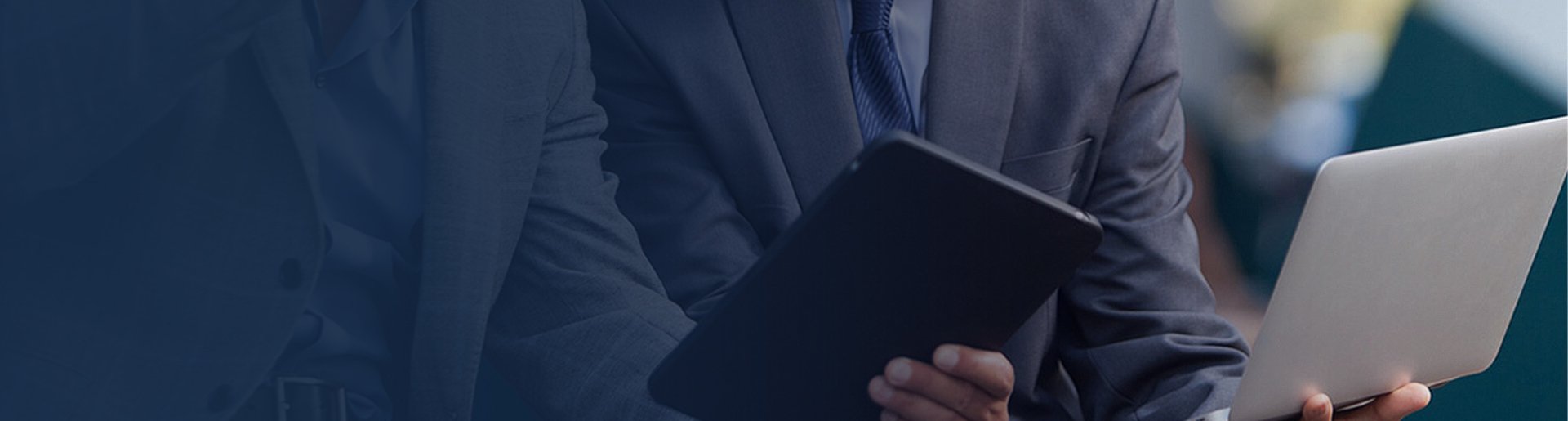
Material selection and process steps of metal deep drawing technology
Material selection and process steps of metal deep drawing technology
The deep drawing process requires high ductility, tensile strength, and formability of materials, and commonly used materials include:
Low carbon steel (such as SPCC, DC04): Low cost, easy to process.
Stainless steel (such as 304, 316): Strong corrosion resistance, suitable for high demand scenarios.
Aluminum alloy (such as 3003, 5052): the preferred choice for lightweight requirements.
Copper and copper alloys: Good conductivity, used for electronic components.
Titanium alloy: high strength and high temperature resistance, used in aerospace.
Process steps
Mold design: The punch, die, and edge ring are key components that need to consider material flow, friction, and rebound.
Preparation of raw materials: Cut the metal sheet to the appropriate size and clean the surface.
Lubrication: Apply lubricant (such as oil, wax, or polymer coating) to reduce friction and wear.
First stamping: The punch presses the blank into the die to form a preliminary shape.
Multiple deep drawing (multi station or continuous die): For high aspect ratio parts, multiple stretching steps are required to avoid material breakage.
Edge trimming and shaping: Remove excess edges and calibrate dimensional accuracy.
Subsequent processing: heat treatment, surface electroplating, spraying, etc.