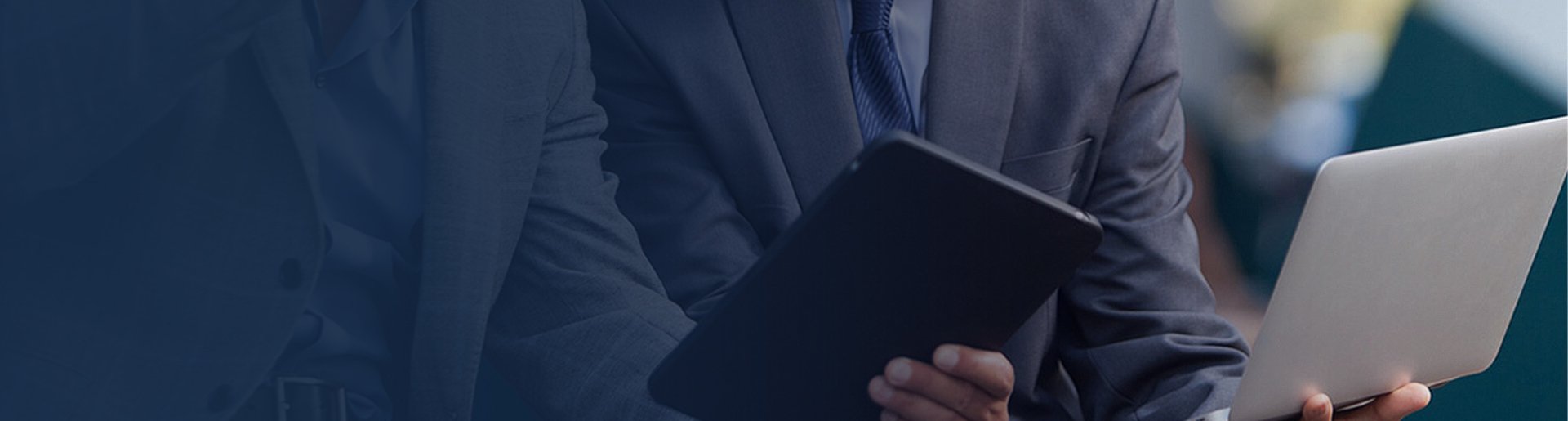
Seam welding parts customization process
In order to meet the requirements of customers, Kailai Machinery has also added the roll welding process, which can meet the welding methods of sheet metal manufacturing and production. Different parts need to be matched with different welding processes to meet the needs of the market. The following will also introduce the principles and methods of the roll welding process for your understanding.
The process of the roll welding head (intermittent) seam welding, each weld point must also go through the three stages of pre-pressing, power heating and cooling crystallization. However, due to the sensitive change of the relative position between the roller electrode and the weldment during seam welding, these three stages are not as obvious as those during spot welding.
1) Under the direct pressure of the roller electrode, the metal being heated by power is in the "power heating period".
2) The adjacent metal that is about to enter the roller electrode is subjected to a certain amount of preheating and some pressure from the roller electrode, and is in the "pre-pressing period".
3) The adjacent metal that has just come out from under the roller electrode is initially cooled on the one hand, and is also subjected to some pressure from the roller electrode at the same time, and is in the "cooling crystallization period".
The welding area under the roller electrode and the metal materials at both ends adjacent to it will be in different periods at the same time. For any welding spot on the weld, the process of passing under the roller is also the process of going through the three stages of "pre-pressing-electric heating-cooling crystallization". Since these processes actually occur under dynamic conditions, the pressure effect during the pre-pressing and cooling crystallization periods cannot be sufficient, so the quality of the seam welded joint is generally worse than that during spot welding, and defects such as cracks and shrinkage cavities are prone to occur.
Roll welding is a solid-state welding method that heats the metal to a certain temperature and then applies pressure with a roller to plastically deform the joint surface to produce metal bonding. This method is most commonly used to produce composite steel plates. The composite steel plate formed by composite rolling using the rolling process is required to have certain mechanical properties such as tensile and bending.
When manufacturing composite steel plates, the surfaces of two thin steel plates are thoroughly cleaned and overlapped with two clean cladding metals in order. The two cladding plates are separated by an infusible compound interlayer. First, the edges of the two middle cladding plates and the two outer steel plates are welded separately to isolate the air and prevent sliding during the rolling process.
The sandwich material is uniformly heated to 1149~1288℃ in a heating furnace. The assembly is then rolled using a roll welding process until the cladding sheet is welded to the base sheet. In addition to welding the cladding sheet to the base sheet, rolling also reduces the thickness of the composite material. After roll welding, the sandwich assembly is separated again to form two composite sheets.