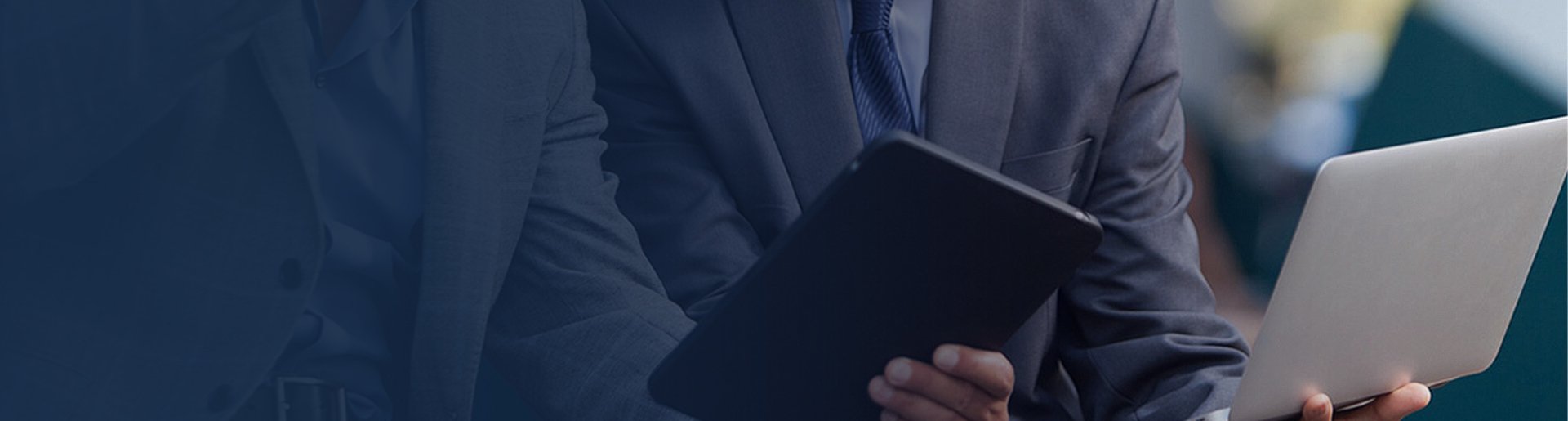
Welding cladding process in sheet metal manufacturing
Welding cladding is a surface coating process commonly used in sheet metal manufacturing. It melts filler materials on the surface of the workpiece to form a uniform and dense coating to improve the surface hardness, wear resistance and corrosion resistance of the workpiece. This article will introduce in detail the welding cladding process in sheet metal manufacturing, including process principles, equipment and materials, process characteristics, advantages and disadvantages, to help readers better understand and apply this important surface treatment method.
1. Process principle:
The welding cladding process uses melted filler materials to form a layer of coating on the surface of the workpiece through a process of high-temperature melting and cooling and solidification. The filling material can be metal welding wire, welding powder, etc. The filling material is melted by the welding heating source (flame, arc, etc.) and coated on the surface of the workpiece to form a coating.
2. Equipment and materials:
a. Welding equipment: including flame blowtorch, arc welding machine, plasma spraying machine and other different types of welding equipment.
b. Filling material: It can be different forms of filling materials such as metal welding wire, welding powder, and welding rods. Select the appropriate material according to different requirements.
c. Auxiliary equipment: including cleaning tools, preheating equipment, etc., used to prepare welding surfaces and improve coating quality.
3. Process characteristics:
a. Uniform surface coating: The cladding process can form a uniform coating on the surface of the workpiece, improving the surface quality and appearance of the workpiece.
b. High surface hardness: The filling material can be selected from metal materials with higher hardness to improve the surface hardness and wear resistance of the workpiece.
c. Good corrosion resistance: The coating can improve the corrosion resistance of the workpiece and extend the service life of the workpiece.
4. Advantages and Disadvantages:
Advantages: Improve the surface hardness and wear resistance of the workpiece, extend the service life of the workpiece, and the surface coating is uniform and beautiful.
Disadvantages: Requires special equipment and materials, higher cost, and higher operating technical requirements.
5. Summary:
As a commonly used surface coating process in sheet metal manufacturing, welding cladding has a wide range of applications and good effects. By rationally selecting filling materials and operating parameters, high-quality and stable surface coatings can be achieved, improving the surface quality and performance of the workpiece, and meeting sheet metal manufacturing applications with different needs.