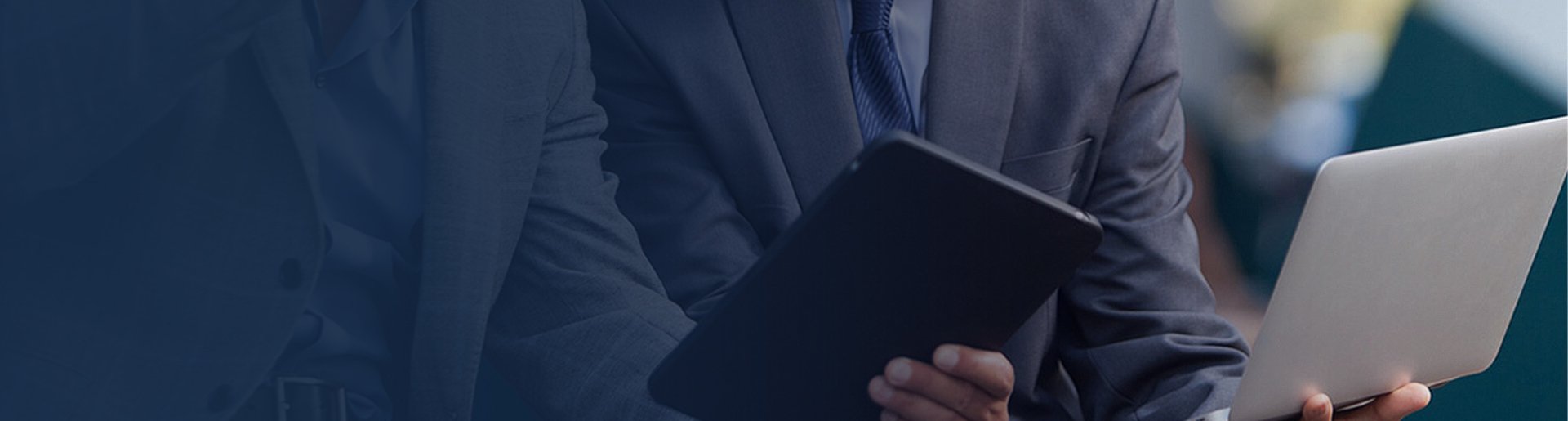
Welding metallographic inspection in sheet metal manufacturing
Welding metallographic testing is a commonly used quality inspection method in sheet metal manufacturing. It evaluates welding quality and performance by observing and analyzing the metallographic structure of the welded joint. This article will introduce the principles, equipment and materials, operation steps and advantages and disadvantages of welding metallographic testing in detail to help readers understand and apply this important welding quality control technology.
1. Principle:
Welding metallographic testing is to observe the metallographic structure characteristics of the welded joint using a metallographic microscope, and judge the quality and performance of the welded joint according to the morphology, size and distribution of the organizational structure. Metallographic analysis can detect defects and abnormal structures in the welded joint, such as inclusions, pores, cracks, etc.
2. Equipment and materials:
The main equipment and materials required for welding metallographic testing include metallographicmicroscopes, grinding and polishing equipment, corrosion reagents, metallographic sample preparation materials, etc.
3. Operation steps:
Preparation: Clean the surface of the welded joint and prepare metallographic samples.
Grinding and polishing: Grind and polish the welded joint sample to make its surface smooth and flat.
Corrosion treatment: The polished sample is corroded to reveal the metallographic structure.
Microscopic observation: The sample is placed in a metallographic microscope to observe and analyze the metallographic structure.
Analysis results: The quality and performance of the welded joint are evaluated based on the morphology, size and distribution of the metallographic structure.
4. Advantages and disadvantages:
Advantages:
The metallographic structure characteristics of the welded joint can be observed intuitively.
Tiny welded joint defects and abnormal structures can be detected.
The test results are accurate and reliable, which helps to discover and solve welding quality problems in advance.
Disadvantages:
The operation is relatively complicated and requires professional technology and equipment.
It has high requirements for sample preparation and processing and is easily affected by the operator's technical level.
It requires a certain amount of time and cost investment.
Summary:
As an important welding quality control method, welding metallographic detection has a wide range of application value in sheet metal manufacturing. By understanding its principles, equipment and materials, operation steps and advantages and disadvantages, we can better master welding metallographic detection technology, improve welding quality and process control level, and ensure product quality and safety.