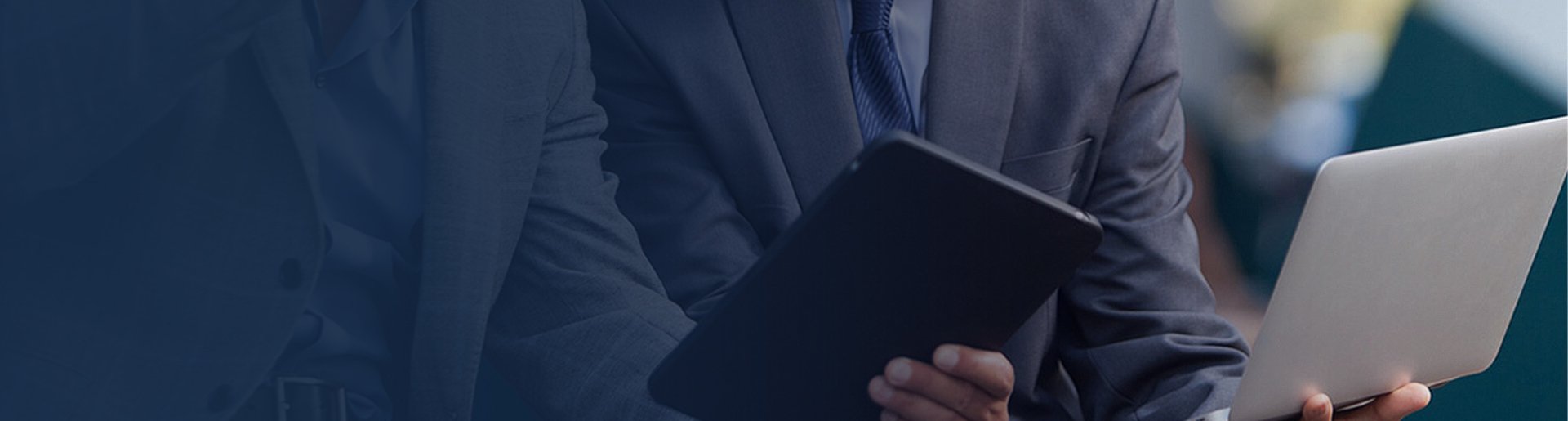
Welding methods of stainless steel materials in sheet metal manufacturing
In sheet metal manufacturing, the welding of stainless steel materials is a key process that affects the quality and performance of the product. This article will introduce in detail the welding methods of stainless steel materials in sheet metal manufacturing, including welding processes, application scenarios, advantages and disadvantages.
1. Classification of welding methods:
The welding methods of stainless steel materials mainly include the following:
a. TIG welding: Also known as argon arc welding, it uses inert gas protection welding, the weld is beautiful, the penetration is small, and it is suitable for occasions with high requirements for welding quality.
b. MIG/MAG welding: It uses inert gas (MIG) or active gas (MAG) protection welding, with a large penetration, suitable for occasions with high production efficiency requirements.
c. Resistance welding: Through heating, pressure and current, two stainless steel materials are welded together, which is suitable for welding thin plate materials.
d. Solder welding: Using solder as a filler material, stainless steel materials are welded together by melting solder, which is suitable for fine welding work.
2. Application scenarios of welding methods:
a. TIG welding: Applicable to occasions with high requirements for welding quality and precise control of welding process, such as aerospace, medical equipment and other fields.
b. MIG/MAG welding: Applicable to mass production and occasions with high requirements for welding efficiency, such as automobile manufacturing, home appliance manufacturing and other industries.
c. Resistance welding: Applicable to welding thin plate materials and occasions where the weld appearance is required to be smooth, such as electronic products, hardware products and other fields.
d. Solder welding: Applicable to occasions where the welding process requirements are not high and the welding parts are difficult to reach, such as microelectronic equipment, toy manufacturing and other fields.
3. Advantages and disadvantages of welding methods:
a. TIG welding: Advantages include beautiful welds and high welding quality, and disadvantages are complex processes, difficult operations and low production efficiency.
b. MIG/MAG welding: Advantages include high production efficiency and simple operation, and disadvantages are that the welding quality is slightly worse than TIG welding, and it is not suitable for occasions with extremely high requirements for welding quality.
c. Resistance welding: The advantages include fast welding speed and low cost, but the disadvantage is that the weld quality is relatively poor and it is not suitable for welding thick plate materials.
d. Solder welding: The advantages are simple operation and low cost, but the disadvantage is that the welding strength is low and it is not suitable for occasions requiring high welding strength.
4. Summary:
In sheet metal manufacturing, choosing a suitable welding method is crucial to ensuring product quality and production efficiency. Different welding methods are suitable for different application scenarios. Enterprises should reasonably choose welding methods according to their own needs and product characteristics, and continuously optimize and improve them in practice to improve production efficiency and product quality.