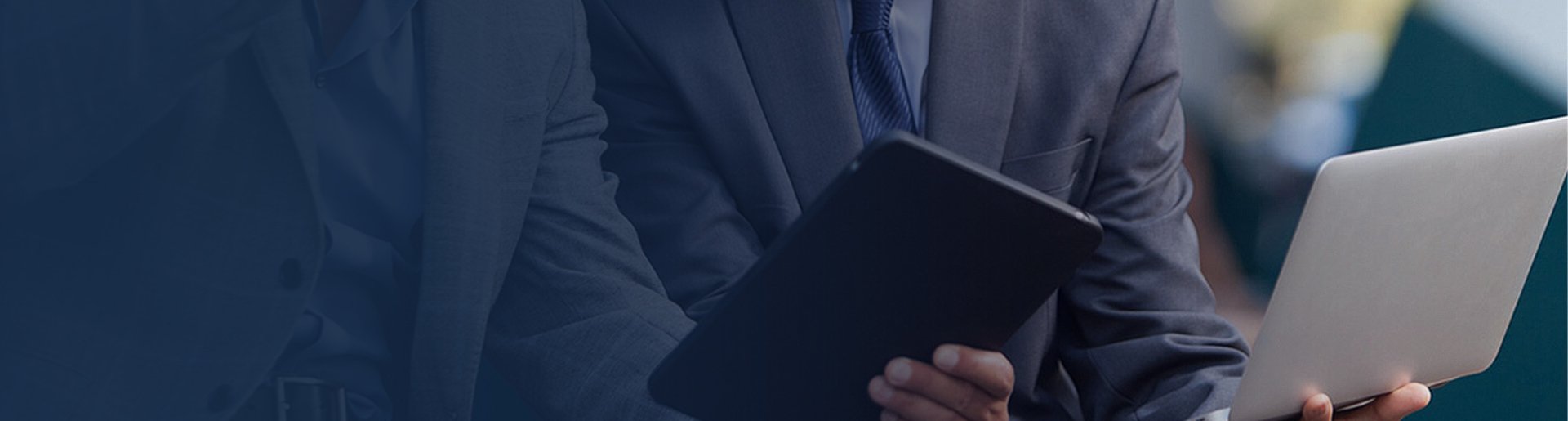
How to weld stainless steel rods to obtain strength that is not inferior to the parent material? — Kailai Machinery’s professional solution
In the automobile manufacturing industry, stainless steel hooks are key load-bearing components, and their welding strength directly affects the safety and durability of the entire vehicle. Kailai Machinery (established in 1996) has 27 years of experience in customizing metal parts. For the welding needs of stainless steel hooks with a diameter of 25mm, it provides a set of scientific and efficient welding process solutions to ensure that the strength of the welded joint is not inferior to the parent material and meet the high standards of the automotive industry.
Stainless steel (especially austenitic stainless steel such as 304 and 316) is widely used in various industries due to its high corrosion resistance and good mechanical properties. However, problems such as hot cracks, intergranular corrosion, and deformation are prone to occur during welding, resulting in a decrease in joint strength. This is a common problem faced by various processing companies. Common factors that affect the strength of stainless steel materials during welding are:
1. Softening of the heat-affected zone: High temperature may cause coarse stainless steel grains and reduce mechanical properties.
2. Welding deformation: Stainless steel has a large thermal expansion coefficient and is prone to deformation during welding, affecting dimensional accuracy.
3. Porosity and inclusions: If the shielding gas is insufficient or the welding material is impure, defects are easily formed and the bearing capacity is weakened.
In response to the above problems, Kailai Machinery uses pulse TIG welding (tungsten inert gas shielded welding) combined with post-weld heat treatment to ensure welding quality:
1. Preparation before welding
Material selection: Use ER308L or ER316L welding wire that matches the parent material to ensure consistent weld composition.
Groove design: V-shaped groove (angle 60°~70°) to ensure uniform penetration and reduce stress concentration.
Cleaning: Use acetone to remove oil stains and avoid welding pores.
2. Welding parameter optimization
Current control: Use direct current positive connection (DCEN), current 120~150A to avoid overheating.
Shielding gas: 98% Ar + 2% N₂ mixed gas to prevent oxidation and enhance weld strength.
Pulse frequency: 5~10Hz, reduce heat input and reduce deformation risk.
3. Post-weld treatment
Solution annealing: water quenching after heating at 1050℃ to eliminate residual stress and restore corrosion resistance.
Mechanical strengthening: shot peening is used to improve surface hardness and extend fatigue life.
Practical application: stainless steel hook case in the automotive industry
The stainless steel hook (diameter 25mm, total weight 10kg) welded this time is used for the automobile chassis suspension system, with a designed load-bearing capacity of ≥500kg. Through the above process, Kailai has achieved:
Weld strength ≥90% of the parent material, verified by tensile test;
No cracks, no pores, and 100% pass rate of X-ray detection;
Dimensional accuracy ±0.5mm, meeting the requirements of automobile assembly.
Welding stainless steel bars is not an easy task, but through scientific processes and strict quality control, Kailai Machinery has successfully solved the welding problem of high-load-bearing hooks in the automotive industry. In the future, we will continue to deepen metal processing technology and provide safer and more durable solutions for global customers.