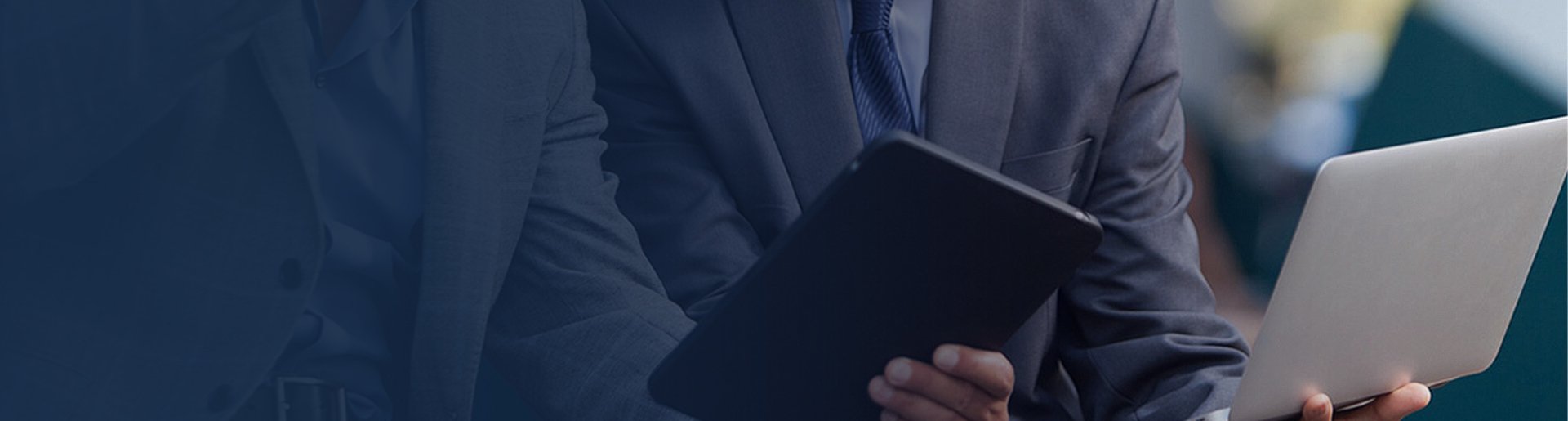
How to solve the problem of thin plate deformation during welding
As a professional metal parts manufacturer, Kailai Machinery has been specializing in the production of metal stamping parts, metal sheet metal parts, laser cutting, metal welding, metal bending parts, metal deep drawing parts and other products for 29 years. There are many welding products among them, and they often face the challenge of thin plate welding deformation during the production process. Welding deformation not only affects product quality, but may also lead to rework and increased costs. Next, I will share with you some effective methods to solve the problem of thin plate deformation during welding.
1. Optimize welding process parameters
Parameters such as welding current, arc voltage and welding speed have a direct impact on the welding heat input, which in turn determines the degree of welding deformation. Generally, the greater the welding heat input, the greater the deformation. To reduce deformation, a smaller welding current and arc voltage should be used, while increasing the welding speed. For example, when welding a 0.5mm thick stainless steel sheet, controlling the welding current to 30-50A, the arc voltage to 18-20V, and the welding speed to 0.2-0.3m/min can effectively reduce the risk of deformation.
2. Choose the right welding method
Different welding methods produce different temperature fields and stress fields, resulting in different welding deformations. Automatic welding heats more concentratedly than manual welding, with a narrow heating zone and less deformation; the two-shield welding wire is thin, the current density is large, the heating is concentrated, and the deformation is small, which is an ideal choice for thin plate welding. When conditions permit, automatic welding and CO2 gas shielded welding are preferred.
3. Reasonable design of welds
Reducing the number of welds and the size of the cross-section can reduce the total amount and distribution of welding heat input, thereby reducing deformation. At the same time, reasonably arranging the weld position so that it is symmetrical to the neutral axis of the weld section or close to the neutral axis can effectively reduce bending deformation. For some thin plate structural parts, welding deformation can also be controlled by reserving shrinkage allowance and leaving space for welding fixtures.
4. Use the reverse deformation method
Before welding, apply a pre-deformation opposite to the welding deformation direction and size to the weldment, which can offset or reduce the welding deformation after welding. For example, when welding a T-joint, bend the wing plate of the weldment upward at a certain angle in advance, and the deformation of the wing plate after welding can be effectively compensated.
5. Rigid fixation method
Apply external rigid constraints to the weldment before welding to force the weldment not to deform freely during welding. For example, when welding a thin plate butt joint, use a pressure iron to press the weldment around to prevent the thin plate from producing wavy deformation after welding. However, it should be noted that this method will cause a large welding stress in the weldment, and it should be used with caution for materials that are easy to crack after welding.
6. Reasonable arrangement of welding sequence
A reasonable welding sequence can evenly distribute the welding stress and deformation on the weldment, reducing or eliminating welding deformation. Generally, welding is done from the middle to both ends or from both ends to the middle to avoid continuous welding from one end to the other end; welding is done from a more rigid part to a less rigid part. For asymmetric welded structural parts, first weld the side with fewer welds, and then use the deformation caused by the more welds on the other side to offset the deformation of the first weld, which can effectively reduce the deformation of the overall structure.
Through the comprehensive application of the above methods, the problem of thin plate deformation during welding can be effectively solved, and product quality and production efficiency can be improved. As a professional manufacturer of customized metal parts, Kailai Machinery will continue to explore and practice to provide customers with better products and services. If you have any needs, please contact us directly.
Email: xxn@lzkailai.com