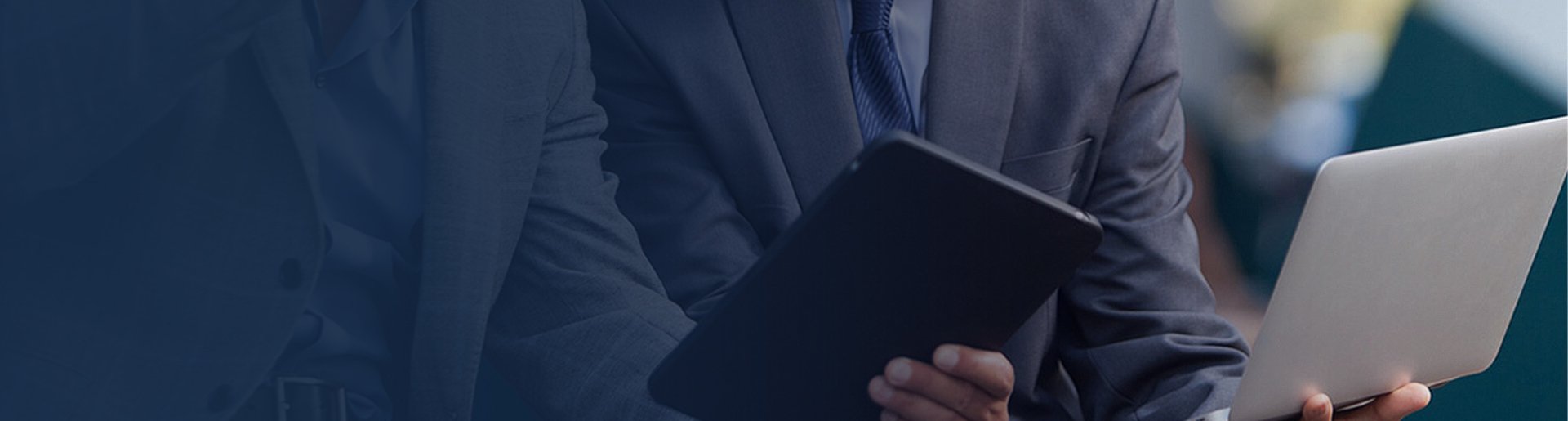
What are the advantages and disadvantages of metal welding?
Advantages of Metal Welding
Connecting metal components through welding processes has multiple welding advantages in terms of strength, durability, and cost. The following are the advantages of this permanent connection technology;
Permanent and durable joint: The strength of metal welded joints is almost similar to that of the base material. In addition, compared to other metal connection techniques such as bonding or riveting, they are very durable. Their lifespan is usually between 10 and 25 years.
Welding of dissimilar metals: Suitable fillers can be used to weld dissimilar metals, such as combinations of aluminum and steel, copper and bronze.
Joint accuracy: Welding techniques such as tungsten inert gas welding can effectively control welding speed and heat input, while maintaining tolerances as low as ± 0.005 inches.
Cost effectiveness: Welding involves fusing two pieces of metal together, which means less material is required to create a joint compared to other methods, resulting in lower overall costs. Meanwhile, its welding speed also helps to reduce costs.
Structural integrity or parts: Unlike bolts and riveting, metal welded parts can maintain their structural integrity without the need for machining or additional processes.
Disadvantages of metal welding
The heat affected zone is the main cost of metal welding processes; The strong heat used to melt the material at the welding position can also affect the thermal properties of the surrounding materials.
Another limitation is thickness, which typically applies to parts larger than 0.5mm.
The skills of the operator seriously affect their skill level.
Vibration in automobiles, industrial process components, and other applications may affect the strength of metal joints.
If you want to learn more about the product in detail, you can click to read the following article or consult us.