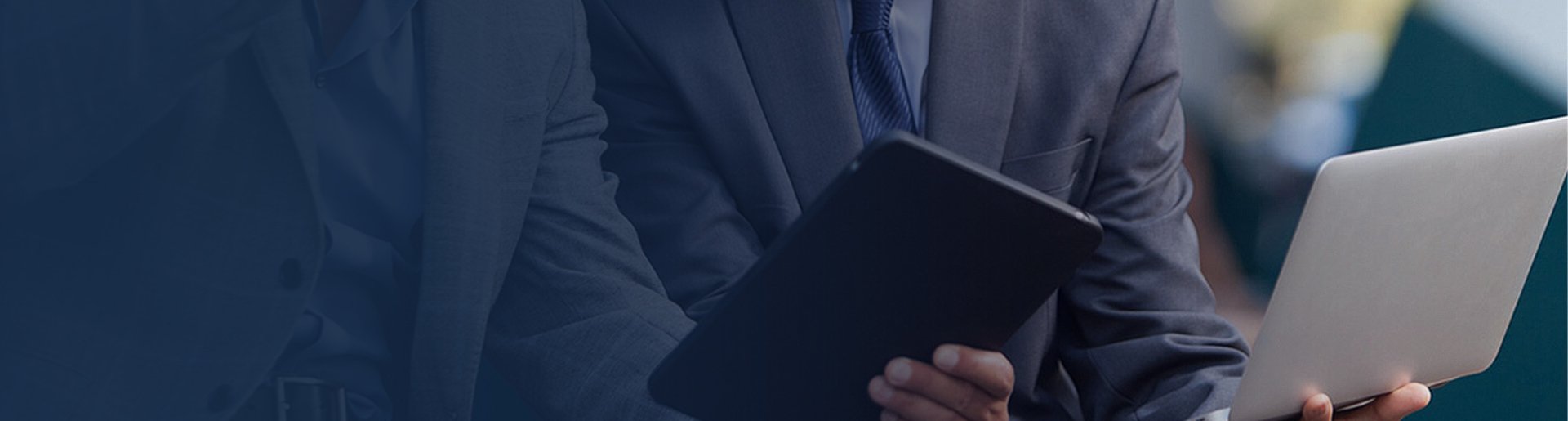
Advantages of Metal Stamping
Advantages of Metal Stamping
1. Cold-Forming Process: As a cold-working technique, metal stamping eliminates the need for heat to shape metals, significantly reducing energy costs and production expenses.
2. Complex Geometries: Enables the fabrication of intricate and sophisticated designs that are unachievable through alternative manufacturing methods.
3. Precision & Repeatability: Exceptional dimensional accuracy and consistency position metal stamping as the premier solution for high-volume component production.
Fundamentals of Metal Stamping
Metal stamping transforms flat metal sheets into precise, custom-designed shapes through a multi-stage process involving advanced tooling and engineering. As a cornerstone of modern manufacturing, it is indispensable across industries—from automotive and aerospace to medical devices and electronics—for producing cost-effective, high-quality components.
RECOMMENDED READING:CUSTOM METAL STAMPING PARTS
Core Techniques
The process integrates specialized operations such as:
- Stamping/Blanking: Cutting metal blanks into predefined contours.
- Embossing/Coining: Creating raised or recessed surface features.
- Bending/Flanging: Forming angular or curved profiles.
Process Mechanics
1. Material Removal: As the punch tool enters the die, excess material (scrap) is sheared from the workpiece, leaving a precisely dimensioned aperture matching the design specifications.
2. Material Compatibility: Primarily applied to sheet metal, though rolled metal stock is also processable.
3. CNC Integration: Modern stamping presses employ computer numerical control (CNC) systems or programmable automation to execute complex forming, casting, and bending operations with micron-level precision.
Industrial Impact
- Speed & Precision: Advanced stamping technologies enable rapid production of intricate metal forms with meticulous dimensional control.
- Material Versatility: Customizable solutions are available for over 300 types of raw materials, optimizing performance for diverse applications.
- Waste Reduction: High-efficiency tooling minimizes material waste while ensuring tight tolerances and repeatability in mass production.