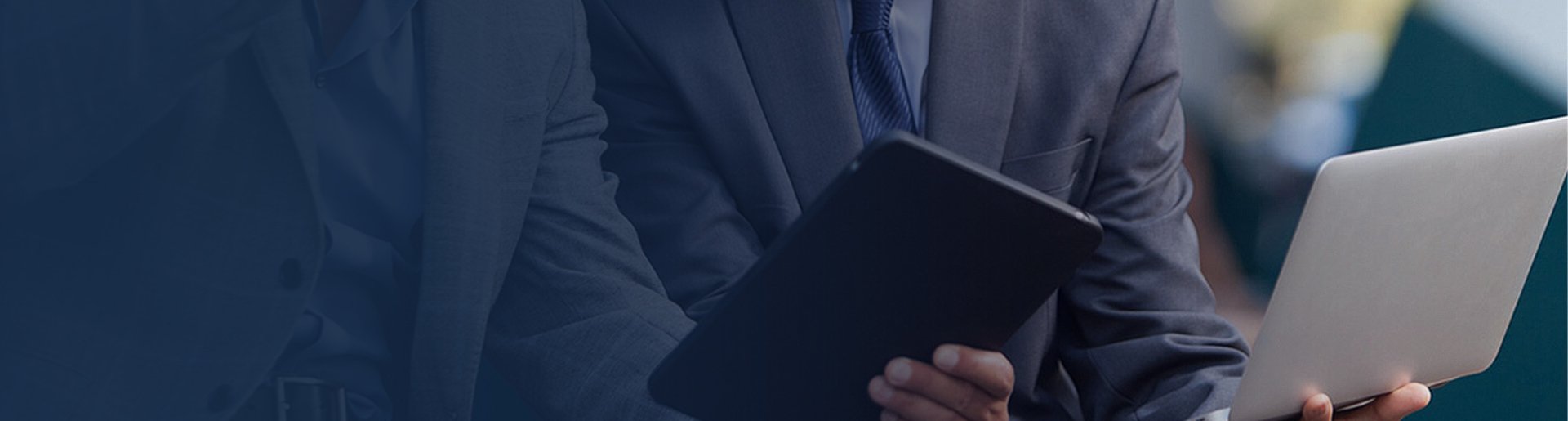
Stamping Process in Metal Fabrication
Stamping, a metalworking technique, involves applying controlled pressure via dies on metal sheets using stamping presses to induce plastic deformation, thereby producing workpieces with precise geometries and dimensions. This process is integral to modern manufacturing, particularly in automotive, home appliance, electronics, and aerospace industries, where it delivers critical functional components.
Key Process Elements
1. Stamping Press: Provides the necessary force and power for deformation.
2. Dies: Define the final shape, tolerances, and features of the workpiece.
3. Sheet Material: Requires optimal plasticity, tensile strength, and thickness uniformity (e.g., steel, aluminum, or specialty alloys).
4. Process Parameters:
- Punching speed
- Applied pressure
- Cycle frequency
These variables directly influence production efficiency, part quality, and dimensional consistency.
Advantages
- High Productivity: Rapid cycle times (seconds per part) enable mass-scale output.
- Material Efficiency Minimal waste due to precision cutting and forming.
- Superior Quality: Excellent dimensional accuracy and repeatability.
- Structural Integrity: Components exhibit enhanced strength and rigidity, suitable for demanding operational conditions.
Limitations
- High Tooling Costs: Complex die design and fabrication require significant upfront investment.
- Economies of Scale: Cost-effectiveness is realized only in large-volume production runs.
This process balances precision engineering with industrial scalability, making it a cornerstone of high-volume metal component manufacturing.
If you want to customize metal stamping parts, please click on the content below。
Custom Metal Stamping Parts