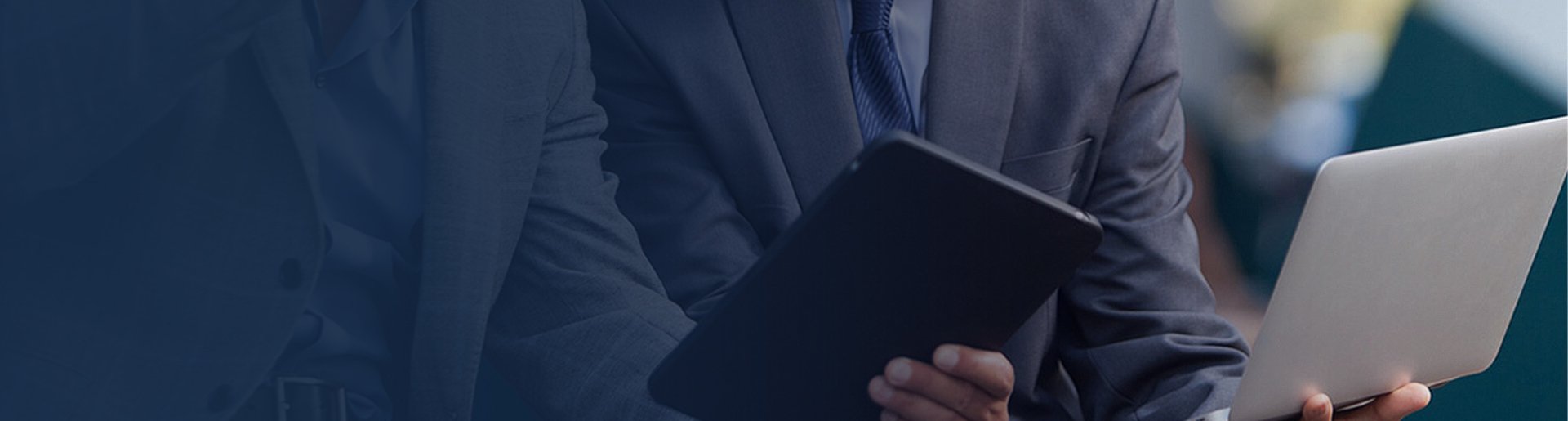
Welding pressure testing in sheet metal manufacturing
The welding pressure test is a commonly used welding quality testing method in sheet metal manufacturing. Welding joints are tested by applying a certain pressure to evaluate their sealing and pressure-bearing capabilities. This article will introduce in detail the principles, equipment and operating procedures, advantages and disadvantages of welding pressure testing, as well as its application and significance in sheet metal manufacturing.
1. Principle:
Welding pressure test is a method that uses pressure to load welded joints and detect whether there is leakage or damage in the joints. During the test, a certain amount of pressure is applied to observe whether leakage or deformation occurs in the joint to determine whether the welding quality meets the requirements.
2. Equipment and operating procedures:
Preparation work: Clean the surface of the welded joint to ensure that the joint is in a clean state.
Equipment preparation: Prepare welding pressure test equipment, including pressure gauges, water pumps or air pumps, etc.
Pressure loading: Place the test piece into the test equipment and apply a certain pressure, usually 1.5 to 2 times the rated working pressure required by the design.
Observation and detection: During the process of applying pressure, observe whether leakage, deformation or other abnormalities occur in the welded joints.
Record data: Record data such as pressure changes, leakage conditions, and test results during the test.
Evaluation results: Based on the test results, determine whether the sealing and pressure-bearing capacity of the welded joint meet the requirements.
3. Advantages and Disadvantages:
advantage:
It can visually detect the sealing and pressure-bearing capacity of welded joints.
The operation is simple and easy to carry out, and does not require complex equipment and technology.
Evaluation results of welding quality can be obtained quickly.
shortcoming:
It cannot fully reflect the quality of welded joints and can only detect surface problems.
Welding joints may be damaged during the test, affecting the use of the test piece.
Not suitable for testing special materials and special welded joints.
4. Application and significance:
Welding pressure testing is widely used in sheet metal manufacturing, especially in the manufacture of pressure vessels, pipelines, fuel tanks and other equipment and components that require sealing and pressure-bearing capabilities. By conducting welding pressure tests, the quality of welded joints can be effectively evaluated, ensuring product safety and reliability, and reducing the risk of accidents.
Summarize:
As a commonly used welding quality testing method, welding pressure test has important application value in sheet metal manufacturing. By understanding its principles, equipment and operating steps, advantages and disadvantages, as well as its application and significance in the manufacturing process, we can better master the welding pressure test technology, improve welding quality and product reliability, and ensure the quality and safety of sheet metal manufacturing products. sex.